冶金厂废气处理是一个综合性的过程,通常包括预处理、主体处理和后处理三个阶段,旨在减少废气对环境的污染。以下是冶金厂废气处理的具体做法:
一、预处理阶段
预处理阶段主要是对废气进行除尘、降温等处理,以减少后续处理设备的负担。
除尘:
干式除尘:使用降尘室、旋风除尘器、布袋收尘器(布袋除尘器对粒径大于0.1μm的粉尘捕集效率可达99%以上,能有效去除细微粉尘,且对粉尘性质适应性强,可处理高湿度、高粘性粉尘)、电除尘器等设备。其中,电除尘器利用高压电场使废气中的粉尘颗粒带电,在电场力作用下向电极板移动并沉积在极板上,从而实现除尘目的,对粒径在0.1~100μm的粉尘具有很高的捕集效率,可达99%以上,尤其适用于处理大风量、低浓度的粉尘废气。
湿式除尘:适用于含湿量大的含尘烟气,常用的湿式除尘设备有水膜旋风收尘器、自激式收尘器和文氏管等。
降温:对于高温废气,可通过冷却装置进行降温处理,以保护后续处理设备并提高处理效率。
二、主体处理阶段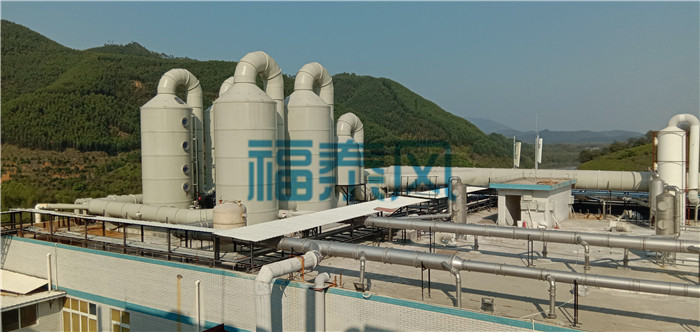
主体处理阶段采用物理、化学或生物方法对废气中的有害物质进行去除。
脱硫:
常用的脱硫方法包括湿法石灰石石膏法(但缺点是设备投资大,运行过程中需消耗大量水资源,会产生一定量的废水,需要配套完善的废水处理系统)、碱性氧化法、活性炭吸附法等。这些方法能有效地将二氧化硫转化为硫酸盐或其他无害物质。
镁法脱硫:以氧化镁或氢氧化镁为脱硫剂,与废气中的二氧化硫反应生成硫酸镁。镁法脱硫具有反应速度快、脱硫效率较高(可达85%~95%)、副产物硫酸镁可用于农业肥料或其他工业领域等优点。相较于石灰石-石膏法,其废水产生量少,对设备腐蚀性较小,但氧化镁成本相对较高,需要综合考虑成本效益。
脱硝:
废气中的氮氧化物也是主要污染物之一,可通过选择性催化还原法(SCR)、选择性非催化还原法(SNCR)等技术进行脱除,将氮氧化物转化为氮气和水蒸气。
重金属离子去除:
对于废气中的重金属离子,可采用冷凝法(对于废气中沸点较高的重金属及其化合物,如汞、铅等,通过降低废气温度,使其凝结为液态或固态,从废气中分离出来)、吸附法(采用活性炭、分子筛等吸附剂吸附废气中的重金属离子)等方法进行去除。
吸附法对低浓度重金属污染治理效果较好,但吸附剂易饱和,需定期再生或更换,成本较高。
挥发性有机物(VOCs)治理:
冶炼废气中的VOCs可通过活性炭吸附法、催化氧化法、热氧化法等方法进行治理。活性炭吸附法利用活性炭的吸附作用将VOCs从废气中去除;催化氧化法和热氧化法则能有效地将VOCs转化为无害物质。
热回收:
冶炼废气中含有大量的热能,可通过余热锅炉、热风炉、热交换器等热回收技术进行能源回收,提高企业的经济效益。
生物处理:
对于一些含有氨气、硫化氢等有机物质的冶炼废气,可通过生物反应器进行微生物降解处理。微生物利用这些有机物质作为碳源和能源进行代谢活动,最终将其转化为无害物质。这种方法具有设备简单、投资少、运行费用低等优点。
三、后处理阶段
后处理阶段主要是对处理后的废气进行二次净化,确保排放达标。这一阶段可能包括进一步的除尘、脱附、催化燃烧等工艺,以确保废气中的有害物质被彻底去除。
四、综合处理工艺组合
考虑到冶金废气的复杂性,单一技术往往难以实现全面达标治理。因此,冶金厂通常采用“预处理+核心处理+后处理”的综合工艺组合来处理废气。例如,废气首先进入高温旋风除尘器去除大部分大颗粒粉尘和炉渣,再进入“电除尘器+石灰石-石膏法脱硫+湿法脱氟”组合处理单元去除细微粉尘、二氧化硫和氟化物等污染物。最后,通过布袋除尘器进行深度除尘,确保排放空气质量达标。
五、注意事项
废气处理设备的选型应根据废气的具体成分、浓度、风量、温度、湿度等参数进行确定,以确保处理效果稳定可靠。
废气处理设备的运行和维护也是确保处理效果的关键环节。冶金厂应定期对设备进行检修和维护,及时发现并解决问题。
在处理过程中产生的废水、废渣等副产品也需进行妥善处理,防止造成二次污染。